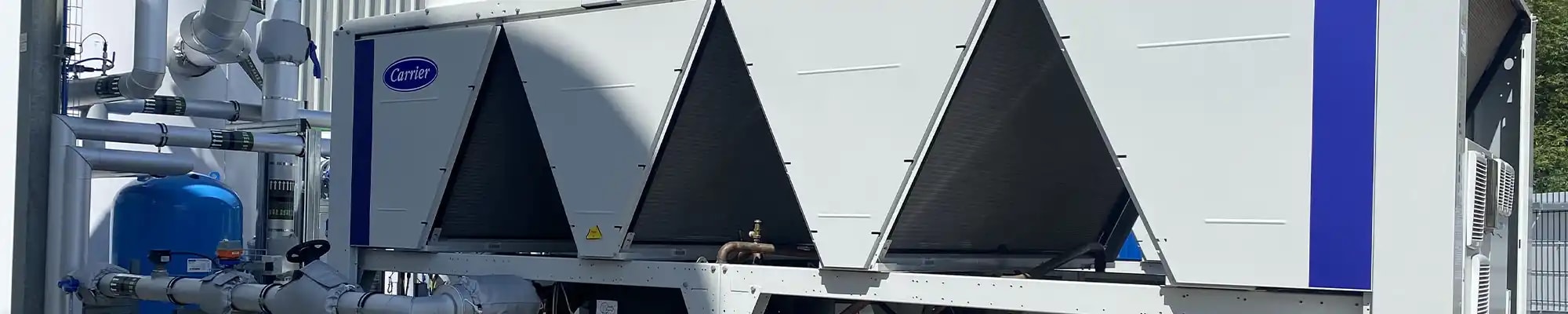
Jones Food Company
Project description
Carrier AquaSnap® 30RBP air-cooled scroll chillers operating on lower global warming potential (GWP) refrigerant R-32 are providing high-efficiency cooling and heating for the world’s largest vertical farm in Lydney located in the Forest of Dean district in Gloucestershire, operated by Jones Food Company.
Named the JFC2, the vertical farm – the size of seventy tennis courts, offers 148,000 square feet of growing space for stacking crops 15 layers high, and is expected to supply 1,000 tonnes of fresh produce a year to UK supermarkets.
It uses 100% renewably-sourced energy to grow crops vertically, including basil, coriander, flat-leaf parsley, dill, green lettuce, Baby Leaf Pak Choi, Bulls Blood, Mizuna, Komatsuna (commonly known as Japanese Spinach), and Baby Leaf Cress (a variety of watercress).
“With our new facility, we further accelerate Britain’s position as a world-leader when it comes to vertical farming,” said James Lloyd-Jones, Chief Executive Officer, Jones Food Company.
“We already supply thousands of British retail stores with basil grown in our first facility in Lincolnshire, but our Lydney site is three times bigger and will allow us to supply a greater range to more stores.”
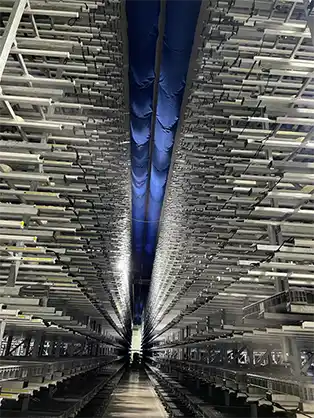
Background
Contractor Brooktherm Refrigeration Ltd was tasked with providing an HVAC solution capable of delivering a constant supply of efficient heating and cooling to the pressurised warehouse.
It was essential that the chillers specified were compatible with Brooktherm’s control system.
“One of the key challenges was the requirement to achieve four different temperature and humidity set points,” said Ben Doherty, Projects Coordinator, Brooktherm Refrigeration Ltd. “With the support of Carrier, we achieved them all.”
Ben Doherty added:
“As well as chillers, we installed four air handling units, hot and cold water tanks, pipe work and valves in the two plants and have since been awarded contracts for three other rooms on the site – a chill store, a process area and a fresh air upgrade.”
Challenges and solutions
Carrier recommended its flexible and compact AquaSnap® 30RBP air-cooled scroll chillers with refrigerant R-32, which operate from -10ºC up to +48ºC, and come with Greenspeed intelligence® variable-speed pumps to reduce pumping energy consumption by up to two-thirds.
The innovative solutions support Carrier’s ESG goal of helping customers avoid more than 1 gigaton of GHG emissions by 2030.
The Carrier chillers have a heat recovery system that enables waste heat to be captured and used for various heating applications on site, saving energy while maintaining optimum growing conditions.
The cultivation warehouse is served by two HVAC plants, one on the north side and one on the south side, each equipped with two Carrier chillers, delivering a total of 2.2 megawatts of cooling and heating to the growing room.
“This exciting project is an efficient and environmentally-responsible way to produce food and Carrier was delighted to be part of such a pioneering, sustainable new approach to growing the nation’s food,” said Paul Hill, Regional Sales Manager, Carrier UK.
“The HVAC plant was fully commissioned summer of 2023, and by October the entire growing area was fully planted, allowing the operator to harvest a tonne in weight of basil and leafy greens every 19 days.”
Carrier’s AquaSnap® 30RBP air-cooled scroll chiller offers an ideal solution for cooling and heating large warehouses.
- Very economical operation
- Efficient coil technology
- Low sound level
- Easy and fast installation
- Environmentally-responsible
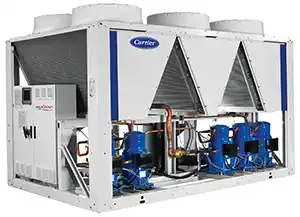