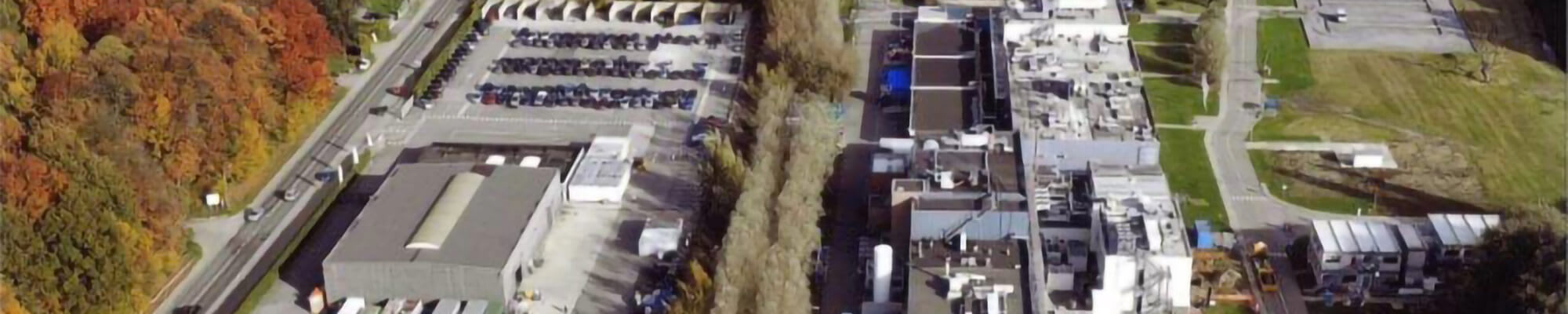
Carrier Supplies Four Chillers To Polypeptide (Belgium)
PolyPeptide is a leading Contract Development & Manufacturing Organization (CDMO). The company focuses on the production of therapies based on peptides and oligonucleotides, supplying pharmaceutical and biotech companies all over the world. PolyPeptide develops and produces the active ingredients for therapies ranging from the treatment of common metabolic diseases, like diabetes or obesity, to cancer and cardiovascular or neurological disorders.
In 2017, PolyPeptide took over a production facility in Braine-l’Alleud, in Belgium. This acquisition was aimed at fulfilling their mission to help clients get approvals from regulatory institutions and successfully launch and sell their products on the market.
The branch in Braine-l’Alleud is intended for GMP peptide production for small right up to large-scale projects. It provides the company with extra liquid-phase capacity (reactor size 6300 litres) and large-scale treatment and isolation options, including industrial-scale spraying and drying for peptide medicines.
The production centre in Braine-l’Alleud employs 280 colleagues and is 172,000 m2 in total – a state-of-the-art plant set-up. After the acquisition, PolyPeptide decided to invest more in the location, especially in improving working conditions for the employees. The temperature in one particular part of the production facility had a tendency to soar in summer. Until recently, this issue was solved by hiring mobile air-conditioning units and placing these at strategic positions throughout the facility, bringing the temperature down to the appropriate level.
Giovanni Morelli of Carrier explains, "This approach certainly works well, but hiring the mobile air-conditioning units every year meant significant costs for the company. After discussions with the employees and the Belgian trade union, the new owner decided to invest in a more permanent solution – installing chillers on a new platform on the ground to provide the building with permanent temperature control for the workspaces."
SPIE Belgium, together with Carrier, helped choose the perfect chillers for the job and took charge of installing all the equipment. Since supply, SPIE has also managed the remote monitoring of the chillers via the production facility’s building management system.
Since the chillers started running in August 2023, the installation has been functioning flawlessly, Alois Callens from SPIE says.
"The cooling system has been very reliable. Any maintenance is carried out on-site as usual. We also integrated the KAZIVE chillers into the production facility’s building management system supplied by Siemens, enabling us to monitor the chillers remotely. That part of the project went without a hitch too. Remote monitoring is now used daily, to ensure that the cooling system is functioning properly and the working conditions on the factory floor stay perfectly within the agreed limits."
Challenges and solutions
Carrier and SPIE chose the AquaForce Vision with the PUREtec™ 30KAVIZE air-chilled liquid chiller with variable speeds and Greenspeed intelligence. This series is the premium Carrier solution for industrial applications, offering exceptional performance and cost-effectiveness. The systems have a small footprint and are easy to install and maintain.
Alois Callens from SPIE explains, "After creating the package of technical requirements, we searched for the best provider. Carrier quickly became the frontrunner for solutions. Together, we then chose four chillers: Two 30KAZIVE0800 with a capacity of 774 kW per chiller and two 30KAZIVE1100, each with a capacity of 1110 kW. This selection means that the 30-by-18-metre space can be kept at the ideal temperature in any season."
One of the interesting benefits of the 30KAXIVE liquid chillers is that they only require small pumps, which makes installation easier. This also results in significantly lower installation costs and energy consumption. Carrier’s Neutral IT system, which was developed to seamlessly connect with the electrical network of the company, ensured smooth installation in an industrial setting. Thanks to solutions like Smart Energy Monitoring and Smart Leak Detection, maintenance and daily monitoring are very easy too.
The 30KAVIZE chillers boast impressive performance. They are up to 10% better than the 2021 (EU) Ecodesign requirements and offer up to 3% performance thanks to the PM motor compressor. Ultrafast capacity recovery maximises energy efficiency by minimising temperature fluctuations in the water circuit.
SPIE didn’t choose the right screw chillers overnight. As the PolyPeptide factory’s long-term technical partner, the firm enquired with multiple producers about technical solutions. The technical collaboration with Carrier seemed to be of such a high quality, however, that the firm quickly chose the 30KAZIVE chillers by Carrier. Especially as Carrier also seemed to be the best partner in terms of cost.
Carrier and SPIE also worked closely together on the installation and commissioning of the four chillers. The project launched in 2022 and was completed in mid-2023.
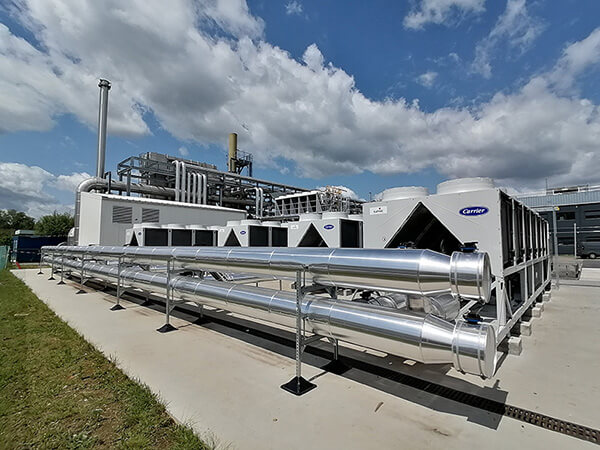
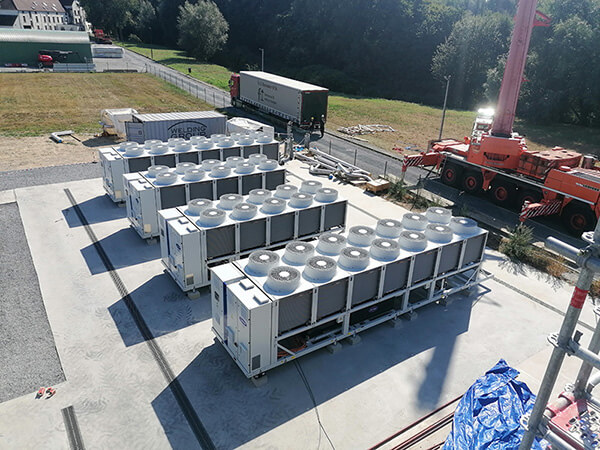
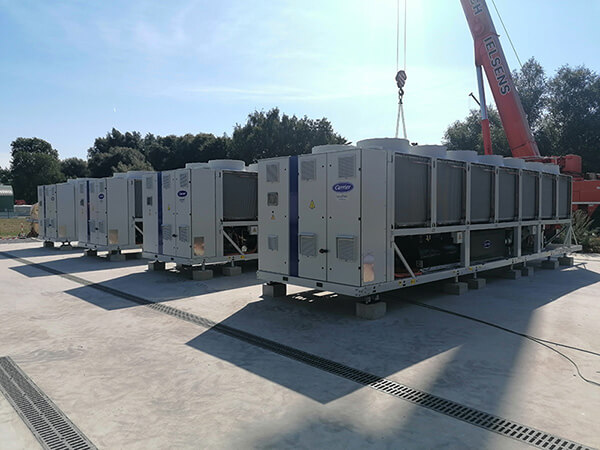
- Ideal work climate
- Lower costs
- Easy management and monitoring
- Reliable
- 2 x 30KAZIVE0800
- 2 x 30KAZIVE1100