TruVu™ ChillerVu™ Chilled Water System Optimizer
TV-OPT
The TruVu Chilled Water System Optimizer is a sophisticated, scalable, native BACnet optimization solution for chilled water plants. The TV-OPT minimizes the energy use of the entire chilled water system, up to and including airside equipment.
The factory-engineered control program is designed to provide advanced chilled water and condenser water setpoint reset, managing the plant chilled water supply temperature and the condenser water supply temperature to provide optimal energy usage while assuring occupant comfort in the building.
The TV-OPT provides seamless integration with the ChillerVu Plant System Manager and is compatible with plants consisting of Carrier 19, 23, or 30 series chillers (air or water-cooled). The system can also be applied to plants featuring third party equipment and controllers, providing the same optimization benefits as are possible with Carrier based plants. An integrated dashboard is also included, providing actionable intelligence to facilities staff, along with real time monitoring of the overall efficiency of the chilled water system, from anywhere at any time using the i-Vu building automation system.
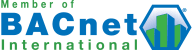

System Benefits
- Compatible with TruVu ChillerVu™ plant manager
- Easy startup and commissioning using the i-Vu user interface
- Fully plug-and-play compatible with the Carrier i-Vu building automation system, seamlessly integrating CWSO’s advanced setpoint reset into the ChillerVu plant control system
- Supports integration to chiller plant equipment using BACnet and Modbus® protocols
- Embedded trends and alarms provide insight into chiller plant performance, and also aid in system tuning, maintenance, and troubleshooting
Energy Savings
- Chilled water setpoint algorithm adjusts the plant setpoint while monitoring and maintaining optimal chilled water system energy consumption
- Dynamic condenser water setpoint algorithm adjusts to maintain optimal tower setpoint, minimizing chiller lift, compensating for ambient conditions and tower approach and providing optimum efficiency
- Intelligent learning algorithms find the optimal energy usage while maintaining comfort conditions
- Adapts “on the fly” to changing environmental and mechanical conditions as well as to changes in facility usage patterns
Software Features
- Supports Metric and English units
- Intuitive pre-built dashboard shows total plant energy usage and key operational parameters at a glance
- Calculates and displays total system energy consumption kWh, peak demand in kW, tonnage, and overall system efficiency in kW/Ton
- Version 3 of the CWSO control program (available for download) adds several key system features, including:
- Savings Assessment Mode – Once initial configuration and tuning is complete, the savings assessment mode allows the system to run one day on/one day off for a user defined period of time for baseline performance verification
- Additional I/O and default Trending to provide greater insight into overall system operation and troubleshooting – highly beneficial for 3rd party plant system applications
- Enhanced System Graphics
Robust Control Features
- Easy, unobtrusive addition to virtually any communicating plant control system
- Optimizes energy consumption across the entire chilled water system; supply and consumption
- Supports system optimization of non-Carrier controlled plants via BACnet and Modbus protocols
BACnet Support | Conforms to the BACnet Building Controller (B-BC), BACnet Router (B-RTR), and BACnet BBMD (B-BBMD) device profiles as defined in BACnet 135-2012 Annex L, Protocol Revision 14 | |
Communication Ports | Gig-E: 10/100/1000 BaseT Ethernet port for BACnet/IP and/or BACnet/Ethernet and/or Modbus TCP/IP communication
S1 Port: High-speed EIA-485 port with End of Net switch for connecting one of the following: » BACnet MS/TP network at 9.6, 19.2, 38.4, 57.6, 76.8, or 115.2 kbps » Modbus RTU at 9.6, 19.2, 38.4, 57.6, 76.8 or 115.2 kbps S2 Port: Electrically isolated EIA-485 port with End of Net switch for connecting one of the following: » BACnet MS/TP network at 9.6, 19.2, 38.4, 57.6, 76.8, or 115.2 kbps » Modbus RTU at 9.6, 19.2, 38.4, 57.6, 76.8 or 115.2 kbps Service Port: 10/100 Base T Ethernet port for system start-up and troubleshooting USB Port: USB 2.0 host port for alternate local access service, device recovery, memory downloads and local EQT displays |
|
Third Party Integration | Supports up to 1,500 third-party BACnet points and 200 Modbus points (memory dependent) | |
Physical | Fire-retardant plastic ABS, UL94-5VA | |
I/O Expanders | Supports up to 9 TruVu MPC I/O expanders and/or 6 MPC Open XPIO expanders (max 9 total) | |
Protection | Two fast acting, 5mm x 20mm glass fuses: • A 2A fuse for the TV-MPCXP’s power • A 4A fuse for the I/O bus edge connector. The power and network ports comply with the EMC requirements EN50491-5-2 | |
Compliance | United States: FCC compliant to Title CFR47, Part 15, Subpart B, Class A; UL Listed, File E143900; CCN PAZX, UL 916, Energy Management Equipment; ANZ: RCM Mark AS/NZS 61000-6-3; Canada: UL Listed File E143900, CCN PAZX7, CAN/CSA C22.2 No. 205 Signal Equip., Industry Canada Compliant ICES-003, Class A; CE Mark Compliant with 2014/30/EU, and RoHS Compliant: 2015/863/EU; UKCA Mark Compliant with Electromagnetic Compatibility Regulations 2016 – Gov.UK and and RoHS for Electrical and Electronic Equipment 2012. | |
Real-Time Clock | Real-time clock keeps track of time in the event of a power failure for up to 3 days | |
Environmental Operating Range | Operating: -40 to 158ºF (-40 to 70ºC) 10 to 95% RH, non-condensing | |
Power Requirements | 24VAC ± 10%, 50-60Hz; 50 VA power consumption; 26VDC ± 10% 15W; Single Class 2 source only, 100 VA or less |
System Benefits
- Compatible with TruVu ChillerVu™ plant manager
- Easy startup and commissioning using the i-Vu user interface
- Fully plug-and-play compatible with the Carrier i-Vu building automation system, seamlessly integrating CWSO’s advanced setpoint reset into the ChillerVu plant control system
- Supports integration to chiller plant equipment using BACnet and Modbus® protocols
- Embedded trends and alarms provide insight into chiller plant performance, and also aid in system tuning, maintenance, and troubleshooting
Energy Savings
- Chilled water setpoint algorithm adjusts the plant setpoint while monitoring and maintaining optimal chilled water system energy consumption
- Dynamic condenser water setpoint algorithm adjusts to maintain optimal tower setpoint, minimizing chiller lift, compensating for ambient conditions and tower approach and providing optimum efficiency
- Intelligent learning algorithms find the optimal energy usage while maintaining comfort conditions
- Adapts “on the fly” to changing environmental and mechanical conditions as well as to changes in facility usage patterns
Software Features
- Supports Metric and English units
- Intuitive pre-built dashboard shows total plant energy usage and key operational parameters at a glance
- Calculates and displays total system energy consumption kWh, peak demand in kW, tonnage, and overall system efficiency in kW/Ton
- Version 3 of the CWSO control program (available for download) adds several key system features, including:
- Savings Assessment Mode – Once initial configuration and tuning is complete, the savings assessment mode allows the system to run one day on/one day off for a user defined period of time for baseline performance verification
- Additional I/O and default Trending to provide greater insight into overall system operation and troubleshooting – highly beneficial for 3rd party plant system applications
- Enhanced System Graphics
Robust Control Features
- Easy, unobtrusive addition to virtually any communicating plant control system
- Optimizes energy consumption across the entire chilled water system; supply and consumption
- Supports system optimization of non-Carrier controlled plants via BACnet and Modbus protocols
BACnet Support | Conforms to the BACnet Building Controller (B-BC), BACnet Router (B-RTR), and BACnet BBMD (B-BBMD) device profiles as defined in BACnet 135-2012 Annex L, Protocol Revision 14 | |
Communication Ports | Gig-E: 10/100/1000 BaseT Ethernet port for BACnet/IP and/or BACnet/Ethernet and/or Modbus TCP/IP communication
S1 Port: High-speed EIA-485 port with End of Net switch for connecting one of the following: » BACnet MS/TP network at 9.6, 19.2, 38.4, 57.6, 76.8, or 115.2 kbps » Modbus RTU at 9.6, 19.2, 38.4, 57.6, 76.8 or 115.2 kbps S2 Port: Electrically isolated EIA-485 port with End of Net switch for connecting one of the following: » BACnet MS/TP network at 9.6, 19.2, 38.4, 57.6, 76.8, or 115.2 kbps » Modbus RTU at 9.6, 19.2, 38.4, 57.6, 76.8 or 115.2 kbps Service Port: 10/100 Base T Ethernet port for system start-up and troubleshooting USB Port: USB 2.0 host port for alternate local access service, device recovery, memory downloads and local EQT displays |
|
Third Party Integration | Supports up to 1,500 third-party BACnet points and 200 Modbus points (memory dependent) | |
Physical | Fire-retardant plastic ABS, UL94-5VA | |
I/O Expanders | Supports up to 9 TruVu MPC I/O expanders and/or 6 MPC Open XPIO expanders (max 9 total) | |
Protection | Two fast acting, 5mm x 20mm glass fuses: • A 2A fuse for the TV-MPCXP’s power • A 4A fuse for the I/O bus edge connector. The power and network ports comply with the EMC requirements EN50491-5-2 | |
Compliance | United States: FCC compliant to Title CFR47, Part 15, Subpart B, Class A; UL Listed, File E143900; CCN PAZX, UL 916, Energy Management Equipment; ANZ: RCM Mark AS/NZS 61000-6-3; Canada: UL Listed File E143900, CCN PAZX7, CAN/CSA C22.2 No. 205 Signal Equip., Industry Canada Compliant ICES-003, Class A; CE Mark Compliant with 2014/30/EU, and RoHS Compliant: 2015/863/EU; UKCA Mark Compliant with Electromagnetic Compatibility Regulations 2016 – Gov.UK and and RoHS for Electrical and Electronic Equipment 2012. | |
Real-Time Clock | Real-time clock keeps track of time in the event of a power failure for up to 3 days | |
Environmental Operating Range | Operating: -40 to 158ºF (-40 to 70ºC) 10 to 95% RH, non-condensing | |
Power Requirements | 24VAC ± 10%, 50-60Hz; 50 VA power consumption; 26VDC ± 10% 15W; Single Class 2 source only, 100 VA or less |